- Energy consumption and environmental impact of baggage handling systems
- Reasons for using sustainable technologies in baggage handling systems
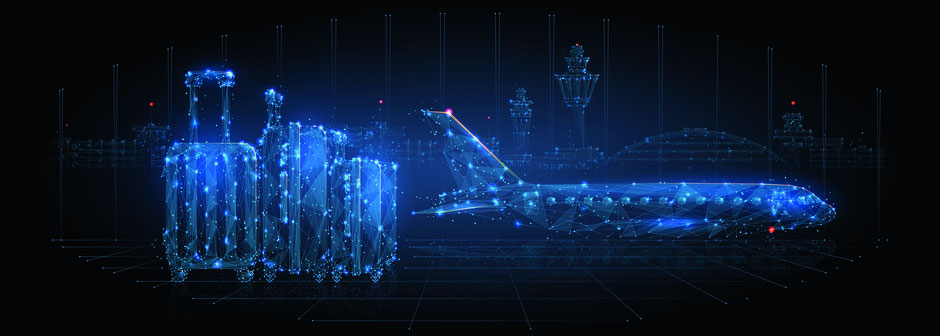
Airports worldwide are once again faced with a growing number of passengers after the slump in passenger numbers caused by the global pandemic. This growth trend caused by globalization will continue in the coming years. The sustainable and environmentally compatible operation of airports, and in particular of baggage handling systems, is therefore of high importance. Undoubtedly, large airports are energy-intensive buildings with an annual electricity consumption of 100 to 300GWh, and within the terminal, conveyor technology is considered the main energy consumer, in addition to building air conditioning and lighting. Accordingly, the sustainable and environmentally conscious operation of baggage handling systems is of particular importance, as these still offer potential for optimization in many cases.
However, there are regional differences in the design of baggage handling systems. For example, international airports usually have frequency inverter-driven systems, while regional airports still have conveyor systems whose motors are operated directly from the mains via contactors and are therefore not energy-efficient. This difference is mainly due to the different passenger volumes in air traffic and the resulting baggage volumes, as well as to economic reasons. For conveyor systems with mains-powered geared motors, the changeover to frequency inverters is basically worthwhile and allows the greatest savings potential for more environmentally friendly and sustainable operation. In order to obtain transparency about the possible savings potential in more modern conveyor systems, the energy requirement of each individual frequency inverter in operation, which converts electrical energy into mechanical movement via a gearmotor, must be determined in order to create a solid starting point for optimizations.
Digitalization is a basic prerequisite for the sustainable operation of a plant. Here, too, modern frequency inverters of the latest generation play an essential role, because they already have the necessary data interfaces. These allow, for example, the energy consumption and energy recovery to be recorded very precisely and made available for further analysis. This makes it possible to compare the real operating data with the theoretical design data and thus already uncovers components of the baggage handling system that are oversized in terms of energy. What sounds simple and logical in many cases, however, often poses a problem because different parties are involved in the design of a conveyor system. The smallest oversizing, perhaps marginal and inconspicuous to one party, can result in the use of larger gearmotors and frequency converters, as the designs available on the market are not step-free for both products. If the required power is determined to be greater than necessary due to oversizing, a 5.5kW frequency inverter is used instead of a 4kW frequency inverter, for example, with correspondingly higher losses. The same also applies to geared motors, since the torques available on the market are also subject to power stages, and power-independent losses occur in the gearbox there. Through sustainable digitalization, such inconsistencies can be detected, and optimizations can be made.
The importance of digitizing drive components for baggage handling systems
- Definition of sustainable and digital technologies and their importance in baggage handling
- Advantages of sustainable digital technologies over conventional technologies
The advancing digitalization and networking of drive components in baggage handling systems offer numerous opportunities for sustainable and ecological development and a contribution to achieving the sustainability goals. The digitalization and networking of baggage handling systems is manifold, but is often templated with the data exchange of individual process data for controlling the motion control, partially enriched with sensor data, and does not do justice to the existing potential in any way.
A drive unit of a baggage conveyor belt consisting of a gearmotor and a frequency inverter which, in simple terms, converts electrical energy into mechanical kinetic energy. Nowadays, the electronics installed in the latest generation of frequency inverters make it possible to record the motor current, which is responsible for the torque and consequently the movement, in high resolution. This is essential as a basis for further data analysis. Based on artificial intelligence algorithms, this motor current can be used to determine anomalies in the operating behavior of the individual conveyor belt, and over the entire conveyor line. The combination of frequency inverter and geared motor can itself be regarded as a high-resolution sensor for anomalies in the conveyor line, which provides raw data and is required per se for the operation of the baggage handling system; there is no need to invest in additional hardware. In initial field applications, artificial intelligence algorithms proved to be a promising approach for detecting anomalies in the system caused by wear and damage to ball bearings and gearing parts of the gearbox.
The challenge here, however, is that most market players are primarily reluctant to use the most modern technologies, which are still being tested. In the past, intelligent fault detection could only be achieved using large volumes of data - so-called Big Data - which had to be obtained from practical applications at great expense and permanently evaluated. However, wear and tear of components that could lead to an unexpected shutdown of the baggage handling system does not usually occur abruptly, but develops over time; accordingly, less data is required, but this data must be of excellent quality and granularity. Small Data colloquially coins this higher quality data set. In order to be able to reliably realize preventive error detection, and thus to get to Smart Data as well as a Digital Twin, the current technology still requires a more time-intensive learning curve. This is mainly due to the fact that each application has its own mechanical characteristics, and a simple generalization is not (yet) possible, but seems to be within reach. An enrichment of the algorithm for preventive error detection with already existing sensor technology, which is available anyway for the smooth control of the baggage flow, is quite conceivable.
However, the simple connection and the exchange of information require a greater integration effort in practice, as there is currently no standardized and organized exchange of information. The Asset Administration Shell (AAS) crystallizes here as a suitable model. It enables and standardizes access to context information of an asset. It contains characteristics of specific functionalities and technical aspects of a product, standardized and semantically unambiguously modeled and stored. Furthermore, information on the Product Carbon Footprint (PCF) is planned, which will provide the user with information on the total greenhouse emissions of a product - which it causes in the various phases of its life cycle. This will make a significant contribution to sustainability. Since this extensive and detailed data represents the product in digital form, this is also colloquially referred to as a digital twin.
The digitalization and networking of baggage handling systems offer numerous opportunities for sustainable and ecological operation, especially when extensive and complex systems are connected and the full potential of digitization is exploited. Economically, the digitalization described above offers improved product utilization, since artificial intelligence will help to maintain or replace components only when anomalies in operating behavior are actually detected.
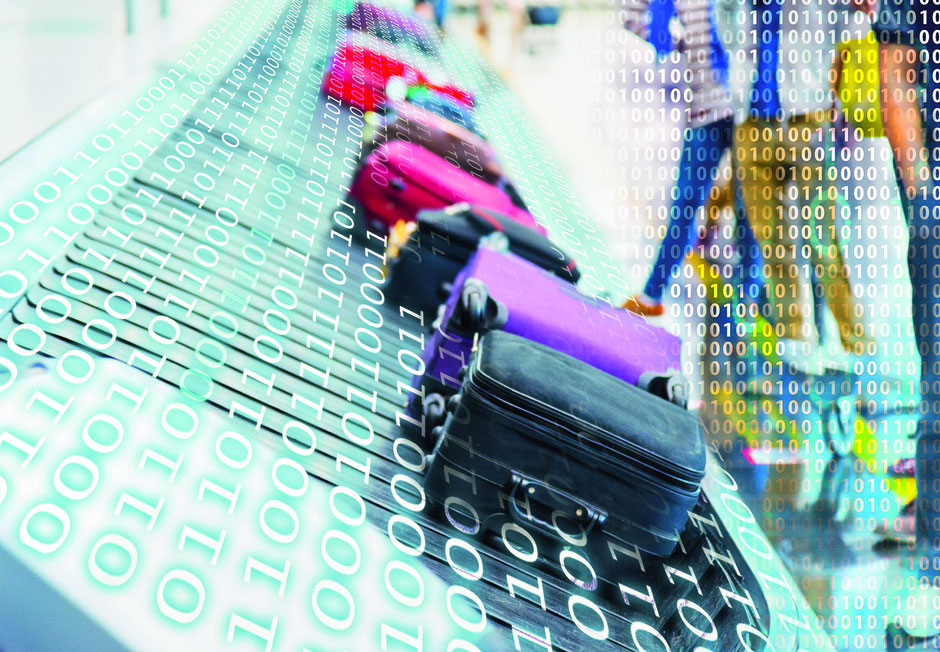
Efficient/sustainable drive motors and their advantages
- Definition of efficient drive motors and their function in baggage handling systems
- Comparison of permanently excited synchronous motors with conventional induction motors
- Sustainability of permanent magnets in PSM and their importance in baggage handling.
In baggage handling systems, the efficiency of the components used is often used as an important component for evaluating their sustainability, but is often interpreted incompletely in the overall context. A better approach is to consistently use the efficiency, which in a baggage handling system results from the energy supplied electrically in relation to the energy dissipated mechanically, and applies equally to each individual component in the system. Mathematically, this results from multiplying the individual efficiencies of the conveyor belt, gearbox, electric motor and frequency inverter. Each individual component has an operating state in which it works particularly effectively, but also operating states in which it is the other way around. The efficiency of a gearbox drops significantly at lower loads, as speed and turbulence losses then increase in percentage terms; the same applies to electric motors in the further partial load range.
Accordingly, efficient conveyor systems can only be designed if the motion profiles and weight loads have been represented as precisely as possible in advance, thereby allowing an individual and tailored design. Tools such as Lenze's Easy System Designer help users determine the best solution for their application. Special characteristics must be taken into account when efficiently designing baggage handling systems, because the energy required to accelerate and overcome static friction can be 400% greater than the 100% power required during constant operation, where only sliding friction must be overcome. In a normal design without taking this into account the induction motor, which are often designed for the nominal torque, must be dimensioned correspondingly larger, which reduces the efficiency per se.
Due to this characteristic feature, the Lenze Smart Motor was developed, which is based on a conventional induction motor, but has an overload capacity of 400%, and can provide the necessary power to set the conveyor belt in motion. In constant operation, the induction motor as well as the gearbox are much closer to the optimal operating point than traditional solutions.
However, the efficiency of the baggage conveyor system can also be increased by state-of-the-art frequency inverters, because traditionally, energy generated during deceleration of the conveyor belt is converted into heat in braking resistors and dissipated thermally. Lenze's i500motec decentralized frequency inverter offers the option of feeding deceleration energy directly back into the grid and making it available to other consumers, and thus has a higher efficiency than commercially available components.
Efficient/sustainable converters and their advantages
- Definition of inverters and their function in baggage handling systems
- Comparison of SiC semiconductors with conventional silicon semiconductors
- Advantages of SiC semiconductors, including their higher efficiency, higher switching frequency and longevity
In baggage handling systems, frequency inverters are used to control and regulate the speed of the baggage conveyor belt of a modern system. For this purpose, a frequency inverter provides the required voltage and frequency at the output as a pulse-pause pattern to control the electric drive, but this method has a negative effect on electromagnetic radiation, which requires cable shielding of the motor cable. This cable shielding has a negative impact on the cost of the motor connection cable, and on installation due to its greater weight and stiffness. If the baggage handling system and its connecting cables extend over longer distances, cost-intensive sinusoidal filters are usually also required to reduce the harmonic content and ensure power transmission.
Silicon carbide semiconductors (SiC), which are still in the pre-development stage, could play an important role in frequency inverters in the future, as they offer promising advantages over conventional silicon semiconductors. The switching frequency of silicon carbide semiconductors (SiC) can be increased to 128kHz, which significantly reduces the pulse-pause pattern at the output of the frequency converter, thereby also significantly reducing spurious emissions without increasing losses within the switching electronics. The improved electrical properties and higher power density of SiC semiconductors allow smaller and lighter designs compared to conventional semiconductors. This even enables the integration of miniature sinusoidal filters, which Lenze has impressively demonstrated in an initial research project based on the i950 servo inverter series, and now provides a harmonic sinusoidal voltage at the output. What may seem technically complex means that users can now use unshielded, less expensive and more flexible motor connection cables, regardless of the required cable length, which reduces installation costs and effort. This novel concept reduces losses by 15% in the entire drive train by eliminating motor-side charging losses, thus helping to conserve resources and reduce operating costs. Currently, however, SiC semiconductors are still more cost-intensive than traditional silicon semiconductors, due to a more complex manufacturing process and still low demand. As SiC technology continues to develop and demand increases, costs will decrease and challenges will be overcome, leading to wider application of SiC semiconductors in converters.
The role of recycling and sustainable materials
- Importance of recycling and sustainable materials in the implementation of sustainable technologies in baggage handling systems.
- Use of recycled materials in the manufacture of drive motors and inverters
- Sustainability of materials, including rare earths in permanent magnets
The role of recycling and the use of sustainable materials was confirmed by the international community as an essential building block in the fight against climate change in the Greenhouse Gas Protocol (GHG) 1998, and is reflected in the respective scopes. Through a continuous and consistent circular economy, indirect emissions within the value chain can be reduced, as emissions generated during raw material extraction, transport and refinement are significantly reduced. A detailed look at the current recycling rates of copper with 17%, aluminum with 40% and rare earths in general with <1%, reveals the potential and the need for action not only from an environmental point of view, but also shows the degree of dependency of the most recent fragile supply chains for the own production site.
Rare earths, of which China is the main exporter, are used in the form of neodymium and dysprosium in high-performance magnets, whose extraction from ores, however, requires complex separation processes. When used within electric drives, neodymium enables a maximally strong magnetic field in a minimal installation space, and dysprosium an improvement in thermal properties, consequently indispensable components for high-performance drives. However, it is difficult to recycle these highly concentrated components, as recycling on an industrial scale is currently only possible to a limited extent, and the recycler often simply lacks the information on the composition of the respective components, which must, however, be provided within the value chain. This problem will become much more acute in the next few years, as the demand for rare earths will increase more than tenfold due to increasing electromobility (EV). What sounds simple and logical in many cases, however, poses not insignificant challenges for industry and politics, which can, however, be solved jointly. To this end, the European Union is working on new regulatory requirements within the framework of the Ecodesign for Sustainable Product Regulation (ESPR), whose declaration of the Product Carbon Footprint (PCF) is intended to provide information about the total greenhouse gas emissions caused by a product in the various phases of its life cycle. For industry, this will in all likelihood mean that it will be obliged to provide certain product information in the form of a Digital Product Passport (DPP). If politicians have their way, the Digital Product Passport will contain information on components, materials and chemical substances, repair capability, spare parts and the proper disposal of a product.
Industry and business have already recognized the need for standardized and organized information exchange along the value chain as a core aspect of Industrie 4.0, and have taken this up in the Asset Administration Shell (ASS). This serves as an abstraction layer and framework format that standardizes access to contextual information about an asset, and its structure a list of submodels in which various characteristics of an asset, such as its specific functionalities and technical aspects, are modeled and stored in a standardized and semantically unambiguous manner. Since this extensive and detailed data represents the product in digital form, this is also colloquially referred to as a digital twin. Individual market participants along the value chain already have extensive information and documentation about their products and components, but these must be stored in a machine-processable, standardized way and with defined interfaces, because only via these standardized interfaces can the market players obtain information about environmental compatibility, and disposal companies obtain the materials used, so that they can then recycle them and return them to the circular economy.
However, the fact that the politically required information would have to be filed as a partial model in the administrative shell, but the main model has not yet been ratified as an industry standard, is not unobjectionable. Furthermore, there is also a foreseeable problem in that not every market player necessarily wants to show in detail how its products are constructed and composed, since conclusions could also be drawn from this about applied techniques and manufacturing processes, and a possible impairment of competitiveness.
Challenges in implementing sustainable technologies and collaboration
- Challenges to implementing sustainable technologies in baggage handling systems, including the cost and complexity of the technologies.
- Importance of collaboration between airport operators and technology providers in implementing sustainable technologies in baggage handling systems.
- Anticipated impacts of sustainable technologies on airport operations and the environment.
In today's world, where sustainability and environmental awareness play an increasingly important role, companies are faced with the challenge of designing their technological infrastructures in a more environmentally friendly and sustainable way. This also applies to baggage handling systems in airports, which play a crucial role in the smooth running of flight operations. The installation of efficient and sustainable solutions is accordingly obvious. What sounds simple and logical, however, turns out to be much more difficult than previously assumed upon closer inspection.
The efficiency of a system is determined by the individual efficiencies of the respective interconnected and networked components, which conversely means that the improvement of an individual component has less effect on the overall system than the large advertised increase in the individual component would suggest. It is therefore essential in complex plants to obtain data transparency about the motion sequences and the energy flow, because this is the only way to achieve targeted optimizations with sustainable technologies, and not just supposed improvements through individual measures. In this context, there is often talk about the acquisition of data from sensors that are inserted externally into the system, but the high-resolution acquisition of the motor current, which on closer inspection is the component that turns electrical current into a mechanical movement transformation, has proven to be by far the most useful data source.
The latest generations of frequency inverters, such as Lenze's latest i500motec decentralized inverter, already provide high-resolution information about energy consumption and its energy recovery. With algorithms based on artificial intelligence, this data can detect even the smallest anomalies from highly complex data, and would thus be useful for increasing the availability of the baggage handling system. The challenge here, however, is that the industry, in comparison with the automotive industry, is primarily passive towards the latest technologies, and is reluctant to embrace technologies that are not fully developed. This is also a problem insofar as the innovation cycles and development times are generally becoming shorter and shorter, which can be excellently derived from the market entries of the VW Golf. While the product life cycle was 9 years immediately after the market launch of the Golf I, this has now been reduced to less than 4 years for the Golf VIII.
The implementation of sustainable technologies in baggage handling systems is undoubtedly a major challenge. A comprehensive analysis of various aspects, from the energy efficiency of the equipment components, the selection of materials with a view to their contribution to the closed-loop economy, their cost and cost-effectiveness over their life cycle, to the integration of the latest technologies, is clearly a complex challenge. Nevertheless, sustainable technologies offer the opportunity to reduce the impact on the environment and contribute to a sustainable aviation industry in the long term.
Guest Author: Tim-Oliver Ricke, Global Segment Manager, Material Handling & Logistics at Lenze SE
Write a comment